Недавно на Магнитогорском метизно-калибровочном заводе «ММК-МЕТИЗ» были
запущены в эксплуатацию и выведены на высокий уровень производительности новые линии по производству калиброванной стали. Это оборудование объединяет в едином потоке операции дробеметной обработки поверхности горячекатаного металла, волочения и правки.
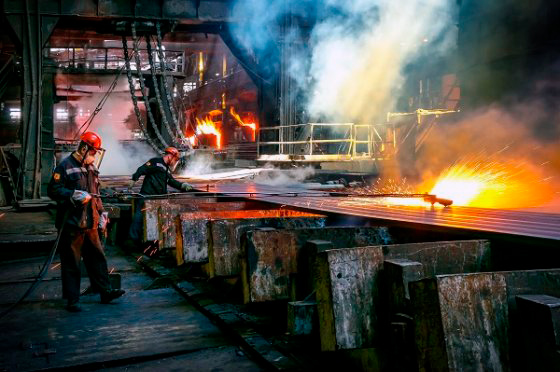
Данный технологический узел был впервые установлен в условиях ОАО «ММК-МЕТИЗ», поэтому при разработке технологии производства на нем большое внимание уделялось исследованиям дробеметной подготовки поверхности.
Для изучения этой технологии на заводе организовали обучающие курсы и пригласили специалистов, владеющих практическими навыками и проектирующих подобные установки. Это помогло лучше разобраться в ряде вопросов и упростить ввод в эксплуатацию нового оборудования.
Основные технические решения, разработанные в ходе освоения новых технологий, были направлены на улучшение условий деформации холоднодеформированных профилей простой и фасонной формы на основе увеличения параметров сцепления поверхности металла со смазочными материалами после дробеметной обработки и проектирования результативных режимов последующей операции волочения.
Технический результат, достигаемый внедрением разработанных мероприятий, заключался в увеличении скорости волочения проката после дробеметной обработки, повышении стабильности и производительности линий по выпуску калиброванной стали EJP CDS 300/80 и DB 800/40 при обеспечении заданного уровня качества готовой продукции.
Для проката из стали марок 10, 20, 35, 40, 45 по ГОСТ 1050 и А12 по ГОСТ 1414 в зависимости от характерного размера прирост скорости волочения составил 20-25%. Для проката из труднодеформируемых марок стали 40Х и 38ХС по ГОСТ 4543, в зависимости от характерного размера круглых и шестигранных профилей, достигнут прирост скорости обработки до 33%.
Помимо освоения и вывода на проектную мощность новых линий по производству востребованной продукции, ММК последовательно проводит политику модернизации и усовершенствования имеющегося оборудования.
Так, в этом году на предприятии
продолжается реконструкция стана 2350. После капитального ремонта здесь будет запущена нагревательная печь № 3. Также прошла полная реконструкция рекуператоров всех печей и заменен газопровод коксового газа. После капитального ремонта всех печей и замены двух мостовых кранов специалистам удалось увеличить объем выпускаемой продукции, при этом процент брака уменьшился с 0,41% до 0,26%.
Продукция, выпускаемая станом 2350, востребована в машиностроении, вагоностроении, применяется для изготовления котлов, сосудов, работающих под давлением. Она пользуется спросом у заказчика и отвечает всем необходимым стандартам качества. За одну смену стан производит порядка 700 т горячего металлопроката. Ширина выпускаемой металлопродукции составляет 2 м, толщина — от 8 мм до 30 мм, длина — 12 м. Путь от заготовки до толстого листа сляб проходит за 10 минут.
Параллельно с модернизацией и производством оборудования для собственных нужд специалисты ММК занимаются разработкой и введением в эксплуатацию новых технических средств для сторонних потребителей. Так, специалисты ООО «Механоремонтный комплекс» (входит в Группу ММК) спроектировали и
произвели линейку импортозамещающего оборудования для ведущих металлургических предприятий России.
Как отмечает директор ООО «Механоремонтный комплекс» Олег Ширяев, предприятие уже освоило производство многих видов оборудования для металлургических производств. Раньше, по его словам, оборудование, необходимое для машин непрерывного литья заготовок, а также детали, узлы и комплектующие, которые используются в листопрокатных цехах, закупались за рубежом.
«Наше предприятие развивается, за счет внедрения новых технологий, развития проектной и технологической базы мы осуществили переход от предоставления ремонтных услуг к исполнению заказов «под ключ» — от проекта до полной его реализации «в железе». Это относительно новый для нас и, как оказалось, очень востребованный подход, который позволяет нам активно заниматься производством импортозамещающей продукции, в том числе для других предприятий металлургического комплекса России», — отметил Олег Ширяев.
Совместно с ГНЦ ФГУП «ЦНИИ Чермет им. И.П. Бардина» специалисты ООО «МРК» изготовили кристаллизаторы МНЛЗ — важнейшие и самые сложные агрегаты машин непрерывного литья заготовок. Одним из заказчиков оборудования выступило АО «ЕВРАЗ НТМК». Для нижнетагильских металлургов также были спроектированы и произведены располагающиеся непосредственно под кристаллизатором агрегаты МНЛЗ — секции 1 с современной централизованной системой смазки и дополнительным роликовым охлаждением.
Помимо этого, ООО «МРК» разработало техническую документацию, осуществило изготовление и серийную поставку в АО «ЕВРАЗ КГОК» спекательных тележек нескольких типов. А для ПАО «ЧМК» были изготовлены роликовые плети для МНЛЗ проекта DANIELI.
Также в этом году ООО «МРК» поставило на сторону спроектированные под заказчика (входящего в топ металлургических предприятий РФ) наконечники кислородных фурм — стратегически важное металлургическое оборудование, без которого невозможно использовать кислородно-конвертерные технологии.
Создавать сложные и высокотехнологичные агрегаты, в том числе с базовыми литыми металлоконструкциями комплексной конфигурации, ООО «МРК» позволяет наличие собственного квалифицированного технологического, проектного и производственного персонала. Кроме того, на предприятии успешно применяют современные технологии с использованием компьютерного моделирования, задействуют линии холодно-твердеющих смесей, современные сварочно-наплавочные и станочные мощности с ЧПУ.
Фото предоставлено управлением информации и общественных связей ММК