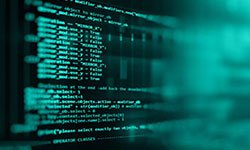
Представители Магнитогорского металлургического комбината (ММК) приняли участие во II международном ИТ-форуме металлургической отрасли Smart Mining & Metals, который
прошел на прошлой неделе в Москве.
ММК на форуме представляли специалисты ПАО «ММК» и ООО «ММК-Информсервис», которые подготовили ряд докладов, приняли участие в дискуссиях и сессиях, посвященных импортозамещению ИТ-технологий и разработке программного обеспечения, цифровому производству и роботизации, работе с данными и беспроводными сетями. Представители комбината поделились опытом реализованных проектов цифровизации ММК и результатами, полученными благодаря применению инновационных технологий.
Директор ООО «ММК-Информсервис» Вадим Феоктистов отметил, что ММК уже имеет высокий уровень автоматизации самых разных процессов, в том числе за счет собственных разработок, и ИТ-ландшафт компании продолжает совершенствоваться в рамках реализации ключевой для комбината стратегии цифровизации. Ее главная задача — обеспечить надежность и производительность используемых и внедряемых программных решений, а также их тиражирование в различные подразделения.
Так, руководитель центра компетенции математического моделирования «ММК-Информсервис» Дмитрий Шнайдер представил на форуме доклад «Оптимальный чугун – комплексная система повышения эффективности первого передела ПАО «ММК» об автоматизированной информационной системе, созданной для оптимального планирования и модельно-упреждающего управления аглококсодоменным производством. Представляя АИС «Оптимальный чугун», он рассказал о ее четырех ключевых модулях: оптимизации привоза и потребления угольного сырья, расчета влияния факторов на режимы работы доменных печей, прогнозирования котировок горячекатаного рулона и оптимального планирования загрузки доменных печей. Также в систему входят блоки прогнозирования цен на сырье и спроса на продукцию.
Кроме того, система может учитывать как универсальные параметры и коэффициенты различных показателей, так и индивидуальные, характерные для конкретной печи, которые уточняются в процессе тестирования. АИС «Оптимальный чугун» обеспечивает глобальную оптимизацию по стоимостному критерию, включая расчет фактического влияния на эффективность доменного процесса различных показателей и режимных параметров работы, расчет плана производства и переменной составляющей себестоимости чугуна, а также интеграцию с системами модельно-упреждающего управления нижнего уровня.
Фактический экономический эффект от эксплуатации отдельных модулей системы в 2021 году составил около 100 млн руб. В настоящее время она проходит этап тестирования и подготовки к вводу в опытно-промышленную эксплуатацию, которая запланирована в августе. В эксплуатацию АИС «Оптимальный чугун» будет введена в декабре текущего года.
Начальник отдела сопровождения и эксплуатации ИТ-инфраструктуры «ММК-Информсервис» Станислав Гордеев рассказал о построении в Группе ПАО «ММК» инфраструктуры промышленного интернета вещей (IIoT) на базе опорных сетей Private LTE и LoRaWAN. Он отметил, что комплекс технологий IIoT позволяет создать среду передачи информации и тем самым обеспечить максимальную готовность ИТ-инфраструктуры для ускорения сроков реализации цифровых проектов различной направленности (цифровые двойники, беспилотный транспорт и автономные роботы, компьютерное зрение).
Основные задачи, решаемые системами IIoT, включают сбор данных с различных устройств и датчиков, их передачу и обмен, позиционирование персонала, оборудования, машин и агрегатов внутри и снаружи помещений, а также узкоспециализированные задачи предиктивной аналитики, распознавания образов. Сейчас на ММК уже подготовлена основная инфраструктура, основанная на российских технологиях и решениях. Они, в частности, позволяют диагностировать неисправности по вибрации, магнитному полю и температуре, а также предвосхищать возникновение и развитие дефектов двигательных установок.
Помимо этого, в рамках форума старший менеджер по оперативно-календарному планированию ММК Александр Фомичев рассказал о разработке системы планирования производства на комбинате. В основу этой работы лег анализ узких мест, оказывающих негативное влияние на эффективность производственного процесса, и задачи по увеличению оборачиваемости активов, снижению себестоимости продукции и повышению качества продукции и сервиса компании.
Для разработки системы управления производством был сформирован список из 18 поставщиков, а план разработки и внедрения системы оперативно-календарного планирования включал в себя шесть основных этапов, охватывающих отдельные производственные цеха ММК. В итоге система планирования производства стала ключевым инструментом мониторинга и управления производством на комбинате. В ней фиксируется своевременность доставки и степень укомплектования заказов потребителей (фактический показатель OTIF по цехам) и динамика выполнения ключевых показателей. Успешная реализация цифрового продукта позволит масштабировать его внутри Группы ПАО «ММК».
Сегодня цифровая трансформация затрагивает все бизнес-процессы ММК, начиная с аглококсодоменного производства и заканчивая взаимодействием с клиентами и потребителями. В основе стратегии цифровизации ПАО «ММК» — около 200 проектов, реализация которых гарантирует безопасность сотрудников, повышает производительность труда и качество продукции.
Так, весной этого года специалисты ММК работали над внедрением
диспетчерского экологического комплекса (ДЭК), который будет обеспечивать постоянный контроль работы природоохранных объектов. С его помощью можно будет в режиме реального времени отслеживать состояние источников выбросов и контролировать соблюдение экологических норм.
Для повышения достоверности и точности определения уровня техногенного воздействия на окружающую среду комбинат ранее внедрил локальные системы в технологическое оборудование. ДЭК же позволит осуществлять непрерывный контроль состояния источников выбросов загрязняющих веществ, вести мониторинг атмосферного воздуха и водных объектов в зоне влияния ПАО «ММК» на окружающую среду, прогнозировать изменение уровня техногенного воздействия на атмосферный воздух Магнитогорска при различных режимах работы технологических агрегатов и в зависимости от технического состояния оборудования и природоохранных объектов.
Внедрение диспетчерского экологического комплекса обеспечит оперативное выполнение персоналом ПАО «ММК» корректирующих управленческих действий в случае превышения норматива выбросов. Это станет очередным важным этапом масштабной работы по снижению техногенного воздействия комбината на окружающую среду.
Кроме этого, ПАО «ММК» успешно
применяет в работе своих предприятий новейшие методы инвентаризации запасов угля и железорудного сырья. Оценку количества сырья проводят с помощью аэрофотосъемки и наземного лазерного сканирования, разработанного компанией SAREX, резидентом «Сколково». Генеральным подрядчиком реализации проекта выступает ООО «ММК-Информсервис».
Новую систему применяют на пяти складах коксохимического и горно-обогатительного производств на территории ПАО «Магнитогорский металлургический комбинат», где находится более 1 млн т сырья. Для получения точных данных специалисты используют разные типы съемки. Для открытых складов применяется аэрофотосъемка, а для закрытых — наземное лазерное сканирование. Съемки выполняются два раза в неделю, на их основании создаются точные цифровые модели складов. Производственные специалисты могут получить доступ к этой информации через web-интерфейс.
По совокупности цифровых данных за определенный период на основе отдельного модуля системы SAREX создаются динамические аналитические отчеты, позволяющие оперативно получать информацию о запасах сырья на любом из складов на конкретную дату.
Одной из главных особенностей внедрения стало то, что система была развернута в закрытом IT-контуре ПАО «ММК» с соблюдением всех требований по информационной безопасности.
Достижения ММК в сфере цифровизации производства в конце 2021 года
были высоко оценены компанией UiPath, мировым лидером на рынке RPA-решений. Комбинат получил награду за вклад в развитие рынка RPA в России и СНГ.
Еще в 2018 году на базе входящего в Группу ООО «ММК-Информсервис» был создан Центр компетенций RPA и инноваций, из которого выросла компания ЦТР «Некст». Уверенно стартовав в 2019 году, масштабный проект по роботизации в 2020 году
охватил все основные функциональные направления, позволив роботизировать свыше 100 бизнес-процессов. Сегодня Центром технологий роботизации «Некст», в котором работают более 40 сертифицированных специалистов, созданы более 250 программных роботов, компания предлагает комплексные проекты RPA под ключ. К числу основных преимуществ программных роботов относится их способность работать в режиме 24/7/365, более высокая скорость, исключение ошибок и влияния человеческого фактора, наличие «цифрового следа» и невысокая стоимость. Средний срок окупаемости проектов RPA — до одного года.
На сегодняшний день ММК планирует на базе промышленного интернета вещей и беспроводных технологий передачи данных кейсы внедрения системы контроля эффективности градирен оборотного цикла турбинного участка ПСЦ, визуализацию схем контактной сети ЖД с системой заявок, энергоменеджмент, системы гиперлокального контроля теплового состояния корпуса доменных печей, системы управления складами и информационную систему входного контроля поставок металлолома.
Изображение предоставлено управлением информации и общественных связей ММК